Products
All Products
Curing
Curing plays a critical role in achieving optimal concrete quality. Our proven systems and technologies ensure precise control over moisture levels and temperatures, resulting in durable, and aesthetically pleasing concrete products.
Customized System Design: Utilizing our simulation software, we can tailor the design of your curing system to match your requirements including:
- Accurate temperature and humidity control
- Correct timing in the curing environment
- Appropriate insulation
- Air circulation
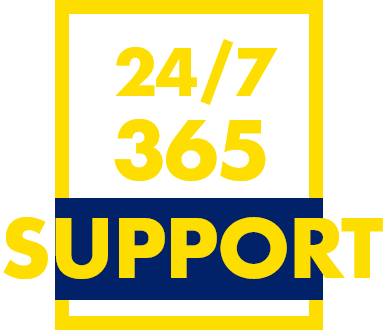
+1.989.354.1000
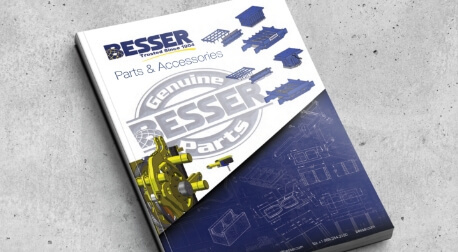