Installation & Service
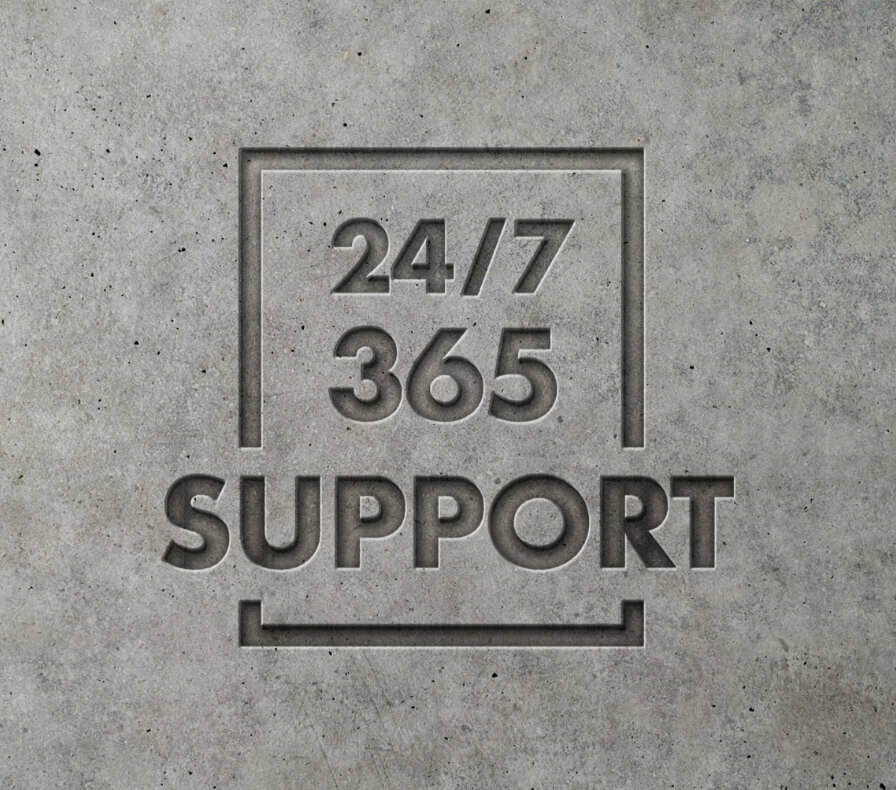
Installation & Service
We understand the importance of keeping your equipment running. Our parts and technical support team is available 24 hours a day, 7 days a week to do just that. Our team travels the world to install your equipment, provide plant evaluations, and support you and your equipment to produce quality products year round.
Contact your Besser Sales Representative for additional information.
24/7 Technical Service and Parts Support +1.989.354.1000
Proactive Customer Support
Providing lifelong, attentive customer service is the cornerstone of Besser Company. Producers using Besser equipment around the globe have 24/7 access to customer support including a worldwide parts supply network, expert technical service, and in-plant training. We pride ourselves in providing industry leading service after the sale to assist producers in maximizing plant efficiencies and profitability.
Services provided include:
- Installation and commissioning of equipment
- Concrete mix and materials analysis to ensure your products meet building codes with optimum strength
- Emergency onsite diagnostics and repair when a breakdown occurs that your staff can’t resolve
Curing Service Contracts
As energy costs continue to increase, Besser works with you to reduce maintenance and energy costs for your curing systems. We provide knowledgeable service technicians that will optimize the performance of your system, improve its efficiency and reduce wasted energy through tuning and optimization that meets local codes.
Plant Evaluations
We’re available to provide cost-effective plant evaluations that will help you maximize the production and efficiency of your concrete products facility. Our technical service representative will travel to your site to evaluate your equipment, procedures, and processes. We will provide you with a written report with opportunities for improvement. We’ll make sure that you’re aware of the ever-changing technology that can positively impact your plant.
Custom Maintenance Programs
Preserving your equipment’s reliability is our goal. Our planned maintenance programs are designed to boost your product quality, maximize your productivity, and minimize your downtime. Through routine inspection of your equipment, necessary adjustments can be made and worn parts can be replaced to prevent downtime.