Products
All Products
Servopac® Family
The Servopac Family of machines has revolutionized the production of concrete units around the world. Four models strong, all members of this family feature operation and adjustments with minimal human touches. The Servopac Family maximizes productivity with:
- Mold & height changes in less than 15 minutes
- Streamlined design for easier maintenance
- Increased mold life
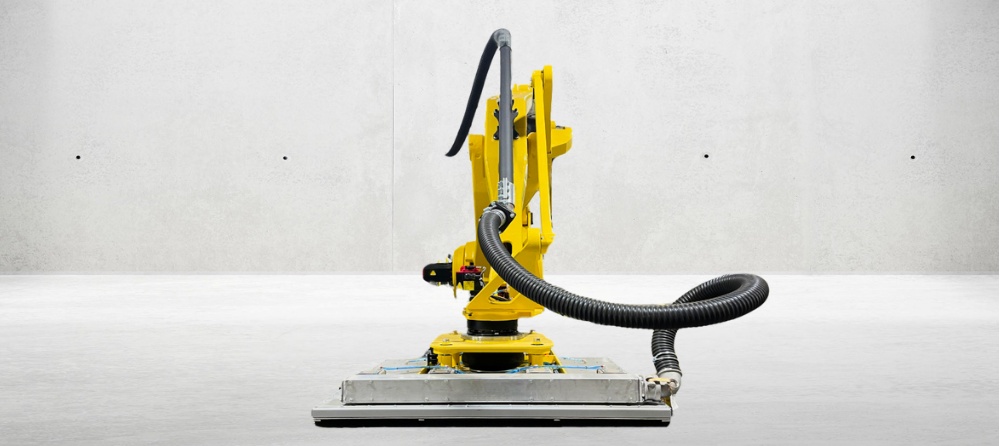
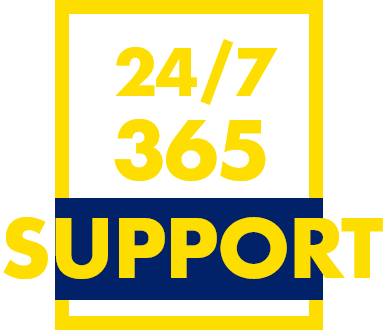
+1.989.354.1000
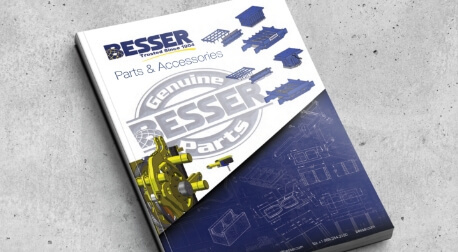