Products
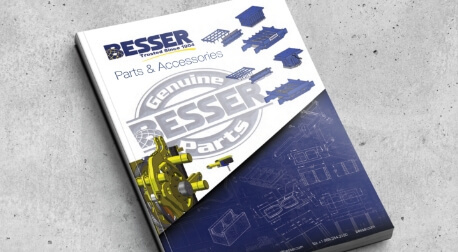
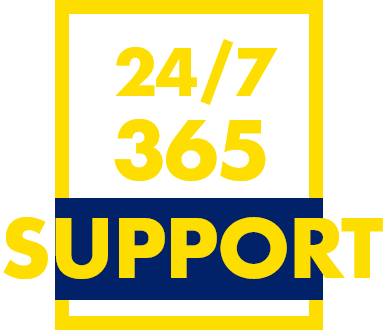
+1.989.354.1000
Revitalize Your Production: Rebuild or Overhaul Your Block Machine's Feedbox and Pipe Machine's Rollerheads!
Need help with equipment, parts, or support?
+1.989.354.4111
Or find your sale representative contact information here.