May 24, 2016
Servopac® Takes Production to New Level at Easton Block & Supply
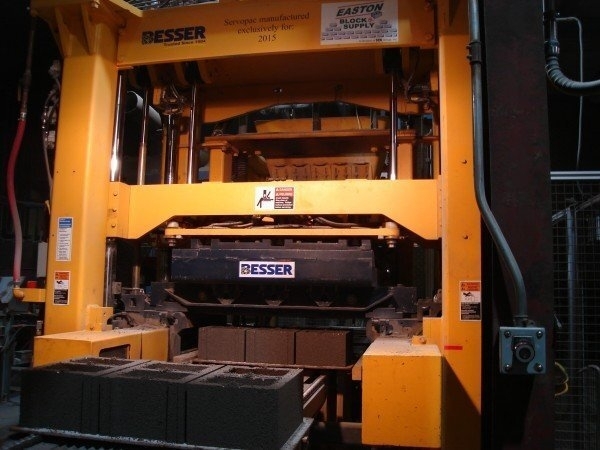
“Mr. Servopac,” as they’ve affectionately named their 2015 four at-a-time model, has put smiles on everybody’s faces at Easton Block & Supply. “We’re totally impressed; Besser covered every base to produce the best machine on the market,” commented Roy Kester, General Manager.The Servopac has operated for nine months, run more than ¾ million cycles, and has yet to break a single mold part. When asked about mold wear, Gary Dunn, Plant Manager, answers tongue-in-cheek, “What mold wear?” The smoothness of vibration is one of the reasons molds last longer. The other reason is the machine is “smart.” “I watched the Servopac shut down to avoid damage from a large piece of aggregate that made its way into the machine,” commented Gary, “had I not seen this with my own eyes I wouldn’t believe it.” The cycle rate of the Servopac has been as high as 8.2 cycles per minute. When producing at this rate, the older handling equipment was struggling to keep up. Today, they’re running at 6.8 cycles per minute to accommodate the handling equipment’s limited speed capability and are still producing 50% more block - of higher quality - than they were able to with their previous competitive machine. The impressive productivity of the Servopac allowed Easton to build their inventory level up during the winter months so that this spring they could reach their goals of increasing sales in their current market area, attracting new customers, and adding more dealers. Beyond productivity there were numerous other reasons that the Servopac was selected for this plant. One was the ability to use existing molds in the machine. According to Roy, “The availability of mold adapters meant we could use existing molds and didn’t need to invest in all new ones. This was a huge cost savings.” Currently their Servopac equipped plant produces standard units. Easton is preparing to move production of architectural and retaining wall units from their Stearns machine to the Servopac once the rest of the plant is upgraded to handle it. The ability to complete full mold and height changes quickly and easily were additional reasons that the Servopac appealed to them, along with its product quality. Easton’s block are testing at 3500 psi, which is well beyond the 2000 psi that the National Concrete Masonry Association (NCMA) cites in their specification and their own goal of 2500 psi. This psi gives them plenty of room to modify the mix design and use less cement and material to save on cost and achieve the same product quality. Before committing to a Servopac, Gary’s only concern was how the fine/sticky aggregate they get from their company-owned quarry would feed. That concern was alleviated when Roy, Gary, Stan Cieslak, Machine Operator, and Terry McNamee, Besser Sales Representative, visited General Shale in Piney Flats, Tennessee and saw a very similar mix successfully being used. The removal of the competitive block machine and the installation of the machine was seamless. Likewise the training of the staff, each with more than 20 years on the job, was easy. Roy recalls, “When they first saw the Servopac panel it was like I was sending 5th graders to college! They learned quickly though and I’m proud of how fast they embraced the new technology and thrilled that they love operating the Servopac.” The staff likes that each cycle is exactly repeatable and that all changes are made from the control panel; there are no mechanical height adjustments. When the operator needs to run a new unit type he completes an initial set up, runs the product, and stores the recipe for the next run. The Servopac makes coming to work so enjoyable, in fact, that Stan has postponed his retirement date! The flawless operation of the Servopac delivers more than high quality block, it delivers peace of mind to Roy and the rest of the staff at Easton. The Servopac’s capabilities have bolstered their confidence and ignited their entrepreneurial spirit so that reaching their goal of being the premier producer in the Mid-Atlantic region by growing the range of products manufactured is within sight. About The H&K Group Easton Block & Supply is part of the H&K Group’s "Family of Companies." This is a group of vertically integrated family-owned and operated companies that together form one of the Mid-Atlantic Region's largest construction materials and full-service site contracting providers. Since 1968, their founding company, Haines & Kibblehouse, Inc., has grown and diversified both horizontally and vertically from a small, local contractor to now include over 80 companies, strategically located throughout central and eastern Pennsylvania, New Jersey, Maryland, and Delaware. The H&K Group Family of Companies plays a critical role in supplying the commercial construction, infrastructure development, and residential building sectors with both contracting services and construction materials. Being one of the region's largest family-owned and operated businesses, they further distinguish themselves with the pride, perseverance, honesty, and dedication that they commit to every customer for every product and service they provide. Learn more about the H&K Group by visiting www.hkgroup.com.
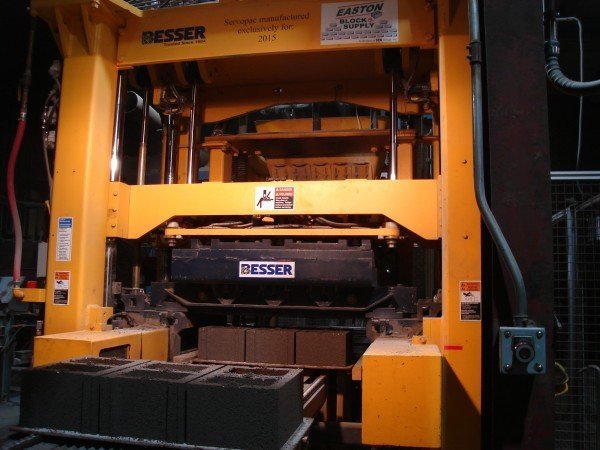
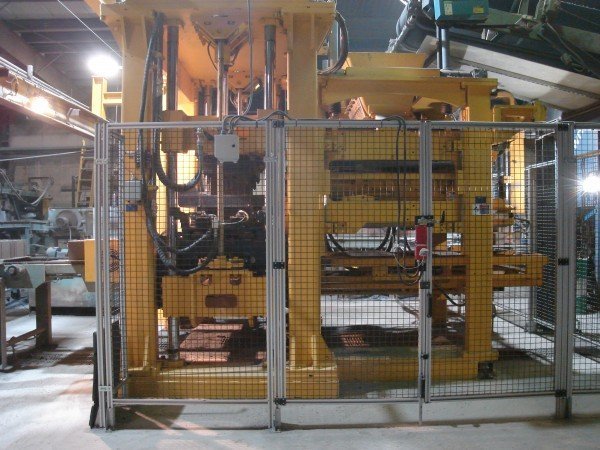