July 29, 2013
Superior Block Builds the World Trade Center
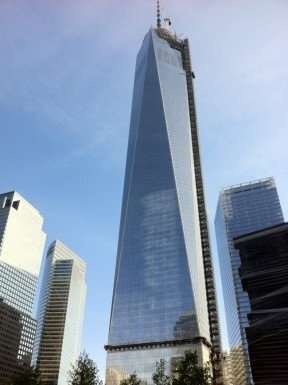
There are few projects in the world that will receive as much global attention as the rebuilt World Trade Center (WTC) towers, transit hub and the new memorial garden. Securing the contract to produce the 1.7 million concrete masonry units for the massive project was a true honor for Superior Block Corporation of Brooklyn, New York. Company Founder and President, Connie Cincotta, shared that this is the third time in her family’s history that they’ve provided units for the WTC. Ajax Block, the company owned by her father, Joseph Cincotta, manufactured the block when the World Trade Center was first built. When it was rocked by an explosion in the 1990s the building was once again reconstructed using concrete masonry units from Ajax.
Then came 9/11 and the World Trade Center vanished. When the new design for the WTC was finalized concrete block were again integral parts of the construction. One of Superior’s longtime customers, Rad & D’Aprile, was named masonry contractor for the project. Company principal, Andrew Feldman, selected Superior based upon the consistent, high quality of their units and their adherence to delivery dates. Connie Cincotta, Superior’s President was consumed with pride when she heard the news. “Supplying units for the World Trade Center, just like my father did when he was in business, means our family’s legacy continues; that means a lot to me.”
The company’s two Besser V3-12 Vibrapacs produced the six, eight and twelve inch units that were specified in regular, medium and lightweight, in hollow and 75% solid configurations. Solite was used to produce the lightweight units while Greenlite, an expanded shale aggregate, was used to produce the “green” units. All concrete masonry units had to meet the specifications for fire resistance that ranged up to four hours.
Production for the WTC was ongoing for four years. Cincotta stated, “The Vibrapacs were the perfect machines for an extended production run like this due to their dependability, ease of operation, and most importantly their ability to consistently produce dense, dimensionally precise units.”
Cincotta equates the selection of Superior’s units for the WTC and other projects to the attention they focus on training their plant staff. That commitment recently involved seven Superior employees traveling to Alpena, Michigan to participate in cutting edge training on electronic controls. “The men who attended the course are experienced machine operators who learned new skills for troubleshooting to further increase production and decrease down time for their plant,” Don MacMaster, Director of the World Center for Concrete Technology and Dean of Workforce Development at Alpena Community College said.
It was during the hands-on session when the crew shared their involvement with the rebuilding project in New York City. Their pride was so contagious the local media interviewed them for an article in the Alpena News which spread the good feeling to residents of the region. “There’s something very special about knowing that you and your neighbors manufacture the equipment that builds and rebuilds the world with environmentally friendly concrete masonry units. Looking into the faces of the crew responsible for the production of the 1.7 million units makes what we do at Besser on a daily basis come to life,” commented Kevin Curtis, President and CEO of Besser Company.
This is the second time this group of Superior Block employees has been to the World Center for Concrete Technology, the first was earlier this year for machine adjustment training.
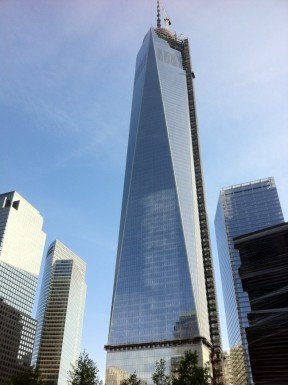
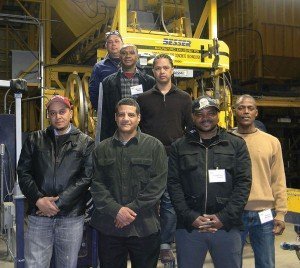